IFOY Test Report: Jungheinrich PowerCube
7th June 2023
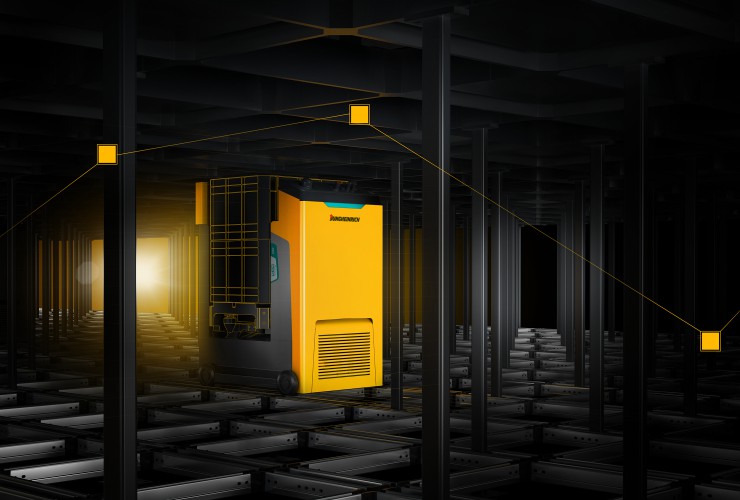
We turn our attention to the Jungheinrich PowerCube as we continue our look at all the IFOY Award finalists ahead of the announcement ceremony in Dortmund on June 22nd.
IFOY category: Intralogistics Robot
More efficient, faster and extremely flexible – as an automated compact storage system for containers, Jungheinrich says the PowerCube sets new standards in warehousing. Through vertical stacking of containers and time-saving storage, retrieval and transfer with high-performance lithium-ion shuttles, the easy-to-integrate warehouse solution ensures efficient processes, impressive space utilisation and a maximum increase in profitability in the era of e-commerce and just-in-time delivery.
IFOY Test Report
Since the storage and retrieval units of the PowerCube automatic compact tote storage system do not drive on top of the tote rack but underneath it, the height of the individual tote stacks can be easily adapted to the respective building infrastructure. Accordingly, it is possible to react to obstacles and, for example, adapt sloping roof shapes to the racking system, which can be up to 12m high.
Another important feature results from the 2D track system on which the shuttles perform their service. The system can be installed on standard industrial floors in accordance with DIN 18202, and floor unevenness can be levelled with levelling feet according to standards.
The maximum load of a container stack is 750kg. Containers designed for the application are used, which can take a load of up to 50kg. The maximum interior size of the containers is designed to allow the transport of standard KLTs (length x width x height: 600 x 400 x 290mm). Jungheinrich might roll out further container dimensions in the future. The PowerCube system containers are compatible with other automation solutions from the manufacturer and can also be used outside the compact storage system with the help of externally connected conveyor technology. Storage and retrieval stations or picking workstations have been implemented accordingly, but could only be visually inspected during the IFOY TEST DAYS, as could the entire system.
The newly developed shuttles move through the plant at a maximum speed of 4m/s and an acceleration of up to 2 m/s/s. The vehicles are designed for the simultaneous transport of two containers. In doing so, the shuttles are able to move automatically at the level below the rack. Since the shuttles operate at floor level, no platform is required to perform maintenance work.
With the help of appropriate relocations, the shuttles reach the containers required to process an order. During the relocations, which are limited due to the storage strategies used, another feature comes into play: The potential energy of the lifted container stacks is used for shuttle recuperation.
Shuttle charging stations are located at the workstations, but can also be installed at other locations within the plant. A fast-charging function creates the conditions for 24/7 operation of the warehouse system. A central element of the vehicles, the number of which can be adapted to the throughput requirements of the respective operator due to their scalability, is the lifting platform. This is shaped in such a way that the container is picked up positively and safely. Any positioning tolerances of the shuttle in both directions of transport can be compensated for by means of a compensation mechanism. As a result, reliable container handling is guaranteed at all times.
IFOY test verdict: Perfect use of space and time: This is how Jungheinrich defines the demands placed on the automated, compact and scalable PowerCube system. The pilot application, a retail company from Switzerland, will show whether the expectations are met. In any case, the potential is there.
IFOY Innovation Check
Market relevance: The market share of compact vertical storage systems has grown steadily over the past 10 years due to their broad applicability in production and retail with low storage space consumption. With the PowerCube, Jungheinrich is addressing a customer segment where storage heights of up to 12m with a variable height profile are desired, e.g., due to sloping ceilings. Since this applies to many existing buildings, the market potential of the solution is high. The economic efficiency is said to be given already from approximately 100 sq m storage area. The first pilot systems are currently being implemented.
Customer benefit: Due to the larger and more flexible warehouse height compared to market leader AutoStore, the PowerCube solution can achieve even better space utilisation. The robots operating underneath the store can transport up to two totes at higher speeds, making them more efficient. They can transfer totes more directly and with shorter access times (approximately two to three minutes) to output stations or conveyor systems. Maintenance is user-friendly at floor level. The installation time of less than six months is good but not exceptional, but extensions can be made almost without interruption during operation. Installation is possible without levelling the floor and different container heights can also be used.
Novelty / Innovation: Although the principle of the vertical compact storage system is not new and no serious differences to AutoStore are to be expected in terms of key figures such as compactness, throughput, costs and energy consumption, access from below is an innovation that permits new forms of use such as variable ceiling height and significantly higher storage bays and simplifies maintenance. Technical innovations in detail are the container loading weight of 50kg, an intelligently designed flap mechanism to hold the container stack in the shaft, a mechanical tolerance compensation for the container pick-up, and a quick-charge function for 24/7 operation of the robots without downtime.
Functionality / Type of implementation: PowerCube is a well thought out and high-quality solution with many potentials beyond the capabilities of AutoStore. The bins have been purposefully redesigned for the solution. Due to the operation from below, the maximum container stack weight is limited to 750kg, though. Energy recovery by the robots takes place during access. However, the system could only be inspected mechanically, not in operation. Use for refrigerated and frozen areas is in the works.
Verdict: The PowerCube vertical storage system, which has been implemented to a very high standard of quality, impresses with the possibility of flexible use of space thanks to variable heights of up to 12m and the use of the robots underneath the storage area, which results in easier maintenance and many options for dispensing goods from the system as well as a connection option to conveyor technology. A high throughput is achieved by the simultaneous pick-up of up to two totes with a load of 50kg each by one robot and its high speed.
Market relevance ++
Customer benefit ++
Novelty / Innovation +
Functionality / Type of implementation ++
[++ very good / + good / Ø balanced / – less / — not available]